ベアリング検査および摩耗測定
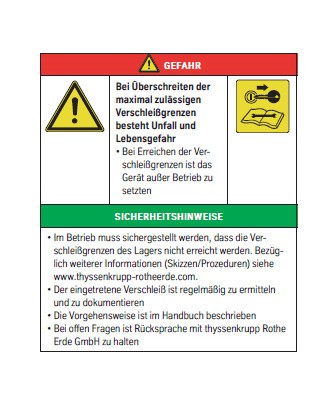
安全上の注意事項 摩耗限界
傾斜クリアランスの測定
傾斜クリアランスの測定
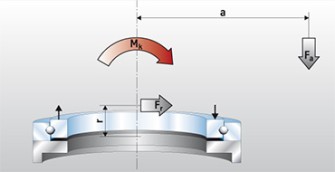
図1:傾斜クリアランス測定の負荷原理(軸方向動作)
可能である場合には、当社は摩耗の特定のために傾斜クリアランスの測定を推奨します。このような測定のための負荷原理は、図1に示されています。
測定は、下側接続構造と上部構造にネジ付けされたベアリング(図2)の間で行います。その際、接続構造の弾性変形の影響を最小限に抑えるため、測定はできるだけベアリングの軌道システムの近くで行う必要があります。
ベアリングの検査 - 損傷の予防
摩耗測定を行うことで、予定外の設備のダウンタイムが発生する前に、技術的な問題を早期に検出することができます。これにより無駄な修理費用とダウンタイムによるの多額の損失を回避することができます。ベアリングの状態を評価するには、当社は、定期的なベアリングの摩耗測定を推奨しています。
軌道システムの摩耗は、軸方向動作の変化または沈降によって確認できます。摩耗の増加は、ケースまたはベアリングタイプに応じて、傾倒クリアランスの測定または沈降測定によって特定することができます。
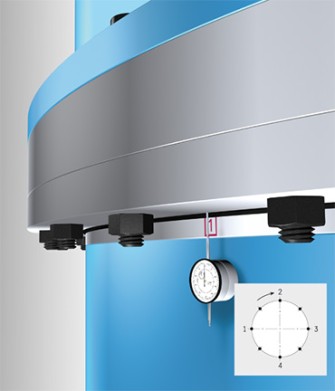
図1:傾斜クリアランス測定の負荷原理(軸方向動作)
プロセスの実施
- 起動時には、基準測定が行われます。
- 指定位置を起点として周辺部の測定点がマークされます。
- 0.01mmの精度を示す必要のある測定器のゼロ設定のためには、まず、最大の巻き戻しモーメントを適用します。次に、必要に応じて負荷をかけることで前向きの傾斜モーメントを生成します。
- 上部構造の旋回後、マークされた測定位置で測定を繰り返します(表4を参照)。
許容されるベアリング遊びの最大増加量(均一な摩耗)
重要:特殊な用途(ティッセン・クルップ ベアリングと確認)については、このベアリング遊びの拡大は許されません。これは、例えば旅客用とでは、記載された値の50%に相当します。
表1:BF*01、08(複列のボールベアリング/アキシャルボールベアリング)
測定プロセス | ボール径 (mm) | ||||||||||
---|---|---|---|---|---|---|---|---|---|---|---|
18 | 20 | 22 | 25 | 30 | 35 | 40 | 45 | 50 | 60 | 70 | |
最大許容摩耗値(mm) | |||||||||||
沈降測定 | 1.6 | 2.2 | 3.0 | 3.8 | |||||||
傾斜クリアランス測定 | 2.5 | 3.0 | 4.0 | 5.0 |
表2:BF*06、09、25、23、28 (ボールベアリング/プロファイルベアリング)
測定プロセス | ボール径 (mm) | ||||||||||
---|---|---|---|---|---|---|---|---|---|---|---|
20 | 22 | 25 | 30 | 35 | 40 | 45 | 50 | 60 | 70 | ||
最大許容摩耗値(mm) | |||||||||||
沈降測定 | 1.6 | 2.0 | 2.6 | 3.3 | |||||||
傾斜クリアランス測定 | 2.0 | 2.6 | 3.2 | 4.0 |
表3:BF* 12、13、19 (ローラーベアリング旋回環)
測定プロセス | ボール径 (mm) | |||||||||||||
---|---|---|---|---|---|---|---|---|---|---|---|---|---|---|
16 | 20 | 25 | 28 | 32 | 36 | 40 | 45 | 50 | 60 | 70 | 80 | 90 | 100 | |
最大許容摩耗値(mm) | ||||||||||||||
沈降測定 | 0.8 | 1.2 | 1.6 | 2.0 | 2.4 | |||||||||
傾斜クリアランス測定 | 1.4 | 2.0 | 2.8 | 3.5 | 4.2 |
表1:BF*01、08(複列のボールベアリング/アキシャルボールベアリング)
測定プロセス | ボール径 (mm) | ||||||||||
---|---|---|---|---|---|---|---|---|---|---|---|
18 | 20 | 22 | 25 | 30 | 35 | 40 | 45 | 50 | 60 | 70 | |
最大許容摩耗値(mm) | |||||||||||
沈降測定 | 1.6 | 2.2 | 3.0 | 3.8 | |||||||
傾斜クリアランス測定 | 2.5 | 3.0 | 4.0 | 5.0 |
表1:BF*01、08(複列のボールベアリング/アキシャルボールベアリング)
測定プロセス | ボール径 (mm) | ||||||||||
---|---|---|---|---|---|---|---|---|---|---|---|
18 | 20 | 22 | 25 | 30 | 35 | 40 | 45 | 50 | 60 | 70 | |
最大許容摩耗値(mm) | |||||||||||
沈降測定 | 1.6 | 2.2 | 3.0 | 3.8 | |||||||
傾斜クリアランス測定 | 2.5 | 3.0 | 4.0 | 5.0 |
表2:BF*06、09、25、23、28 (ボールベアリング/プロファイルベアリング)
測定プロセス | ボール径 (mm) | ||||||||||
---|---|---|---|---|---|---|---|---|---|---|---|
20 | 22 | 25 | 30 | 35 | 40 | 45 | 50 | 60 | 70 | ||
最大許容摩耗値(mm) | |||||||||||
沈降測定 | 1.6 | 2.2 | 2.6 | 3.3 | |||||||
傾斜クリアランス測定 | 2.0 | 2.6 | 3.2 | 4.0 |
表2:BF*06、09、25、23、28 (ボールベアリング/プロファイルベアリング)
測定プロセス | ボール径 (mm) | ||||||||||
---|---|---|---|---|---|---|---|---|---|---|---|
20 | 22 | 25 | 30 | 35 | 40 | 45 | 50 | 60 | 70 | ||
最大許容摩耗値(mm) | |||||||||||
沈降測定 | 1.6 | 2.2 | 2.6 | 3.3 | |||||||
傾斜クリアランス測定 | 2.0 | 2.6 | 3.2 | 4.0 |
表3:BF* 12、13、19 (ローラーベアリング旋回環)
測定プロセス | ボール径 (mm) | |||||||||||||
---|---|---|---|---|---|---|---|---|---|---|---|---|---|---|
16 | 20 | 25 | 28 | 32 | 36 | 40 | 45 | 50 | 60 | 70 | 80 | 90 | 100 | |
最大許容摩耗値(mm) | ||||||||||||||
沈降測定 | 0.8 | 1.2 | 1.6 | 2.0 | 2.4 | |||||||||
傾斜クリアランス測定 | 1.4 | 2.0 | 2.8 | 3.5 | 4.2 |
表3:BF* 12、13、19 (ローラーベアリング旋回環)
測定プロセス | ボール径 (mm) | |||||||||||||
---|---|---|---|---|---|---|---|---|---|---|---|---|---|---|
16 | 20 | 25 | 28 | 32 | 36 | 40 | 45 | 50 | 60 | 70 | 80 | 90 | 100 | |
最大許容摩耗値(mm) | ||||||||||||||
沈降測定 | 0.8 | 1.2 | 1.6 | 2.0 | 2.4 | |||||||||
傾斜クリアランス測定 | 1.4 | 2.0 | 2.8 | 3.5 | 4.2 |
ギアの点検
ギアの点検
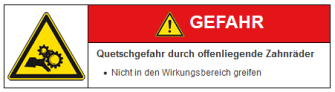
挟み込みの危険に関する安全上の注意書き
使用期間中には、歯の平滑化や摩耗が発生します。許容摩耗限界は、個々の用途に大きく依存します。経験に基づくと、許容される摩耗は歯面あたり最大0.1xモジュールとなっています。
沈降測定
沈降測定
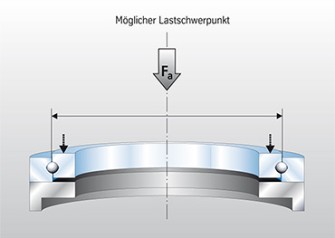
図3:沈降測定の負荷原理
傾倒クリアランスの測定が不可能な場合は、沈降測定を推奨します。その際、負荷の組み合わせの重心は、ベアリングの軌道円直径の内側にあります。負荷原理は、図3に示されています。
測定は、下側接続構造と上部構造にネジ付けされたベアリング(図4、5)の間で行います。
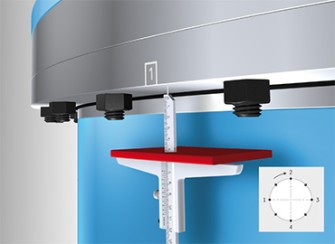
図4:深さゲージによる沈降測定の基本構造
手順は、傾斜クリアランスの測定と同様です。
- 装置の起動時には基準値が決定されます。
- 指定位置を起点として周辺部の測定点がマークされます。
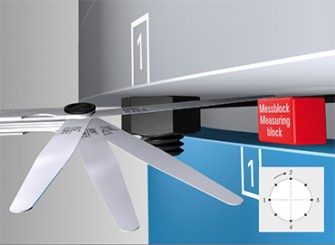
図5:隙間ゲージによる沈降測定の基本構造
ベアリング固定ネジの点検後、適切な間隔で傾倒クリアランスおよび沈降測定を同じ条件下で実施する必要があります。基準測定と比較して違いがある場合は、摩耗が発生していることを意味しています。摩耗が増大している場合には、より頻繁に測定する必要があります。
そのメリットは次のとおりです: ベアリングの状態の明確な評価によって、摩耗した部品を適時に交換することができます。これを最適なスペアパーツ管理と組み合わせることで、損害や長期間にわたるダウンタイムを回避することができます。
ご注意: 許容摩耗値を超えた場合、装置の使用を停止されることを推奨します。
代替方法: 内蔵式摩耗測定装置(IWM)
設備の機能性と運用上の安全性をさらに最適化するために、ティッセン・クルップ ベアリングは常時状態監視のための革新的なソリューションの開発に取り組んでいます。旋回ベアリング用内蔵型摩耗測定装置は特許登録された発明です。これにより、軸方向の最大許容遊びやベアリング旋回環の沈降のオンライン監視が可能となします。
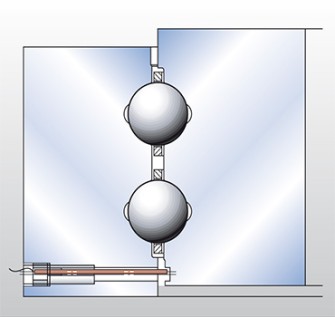
図6:ボールベアリングにおける摩耗測定
そのメリットは次のとおりです: 軸方向の遊びを検出するために作業を中断する必要はありません。
軌道のピーク負荷の領域にはステンレススチール製のピンがあります。これは、電気的に絶縁され、環に取り付けられています。ピンは、カウンターリング内の溝に向けて突き出ています。許容される最大遊びは、溝幅によって調整することができます。
許容できないレベルまで遊びが変化する場合は、環とピンが接触します。ピンの電気接続によって、ピンの対抗環への接触によって信号がトリガされます。この信号は、環の許容相対変位に達しており、ベアリングの検査が必要であることを示します。
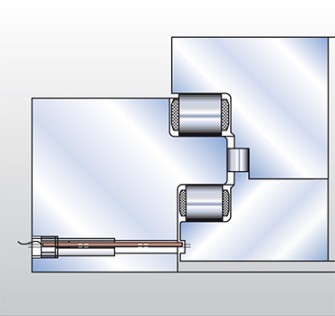
図7:ローラーベアリングでの摩耗測定
そのメリットは次のとおりです: 接続構造の変形やネジ接続部の弾性は、測定結果にそれほど影響を及ぼしません。
弾性による軌道の接近、ベアリングの軸方向の遊び、そして取り付け面の平坦度偏差は補正されます。これにより保守作業者のための費用は最小限に抑えられます。
グリースサンプル採取
グリースサンプル採取
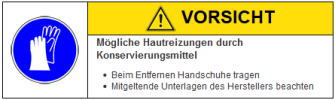
防腐剤による皮膚の炎症に対する警告
グリースサンプル採取セット
グリースサンプル採取セット
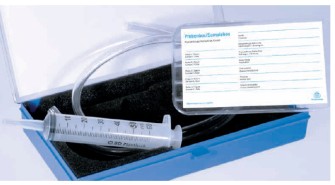
図8:グリースサンプル採取セット
検査測定と同時に使用済みグリースのサンプルが採取されます。使用済みグリースの分析は、軌道の状態に関するさらなる情報を提供します。
グリース採取穴付きベアリング
グリース採取穴付きベアリング
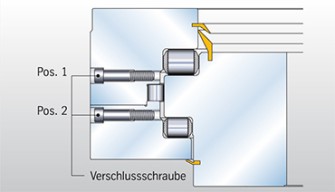
図9:グリース採取穴付き3列ローラーベアリング旋回環
グリースサンプル採取キットには、プラスチック製チューブ、各種封止キャップ、吸引装置と5つのグリースサンプルを収容できるサンプルボックスおよび取扱説明書が含まれています。手順を詳細に説明します。
グリースサンプルは、主に負荷がかかる部分から採取する必要があります。
サンプル採取のために選択した封止ネジ(M16 EN ISO 4762)を取り外します(図9および10: 位置1および必要に応じて対向側、位置2)。
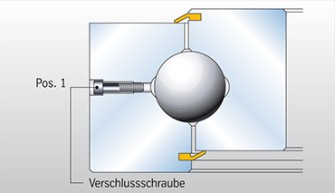
図10:グリース採取用穴を持つ単列ボールベアリング
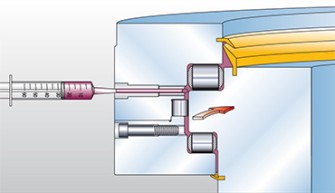
図11:採取
グリースサンプルの採取前に、付属のチューブをグリース採取穴の全長よりも少しだけ長目に斜め(45°)に切断してください。チューブは、所定の穴(図11)に軌道領域まで挿入してください。
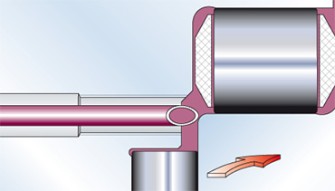
図12:採取部の詳細画像
その際、45°切断面を回転方向とは逆に配置する必要があります(図12)。
採取用穴は封止ネジで再び閉めてください。
グリースを採取した後には、ホースの両端をプラスチック製キャップで封止します。
グリースのサンプルは番号を付け、マークされたサンプルボックスに保管します。
サンプルボックスの上部には、必要な情報が記載されています(グリースサンプル採取キット、図8を参照)。
グリース採取穴なしベアリング
グリース採取穴なしベアリング
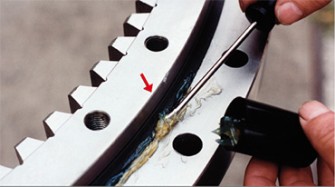
図13:シールリップでのグリース採取
ベアリングにグリース採取穴がない場合、シールにおいて1つまたは複数のグリースサンプルを採取します。この領域は、グリースニップルの近くでクリーニングされます。できれば、採取はメイン作業領域および/または180°のオフセットで行うようにしてください。
前述のグリースニップル(ベアリングの回転なし)での再潤滑中は、シールリップから最初に出てきたグリースを採取します(図13)。採取量は3ccで十分です。
ご注意: 汚染によって間違った結果とならないよう、採取は慎重に行ってください。
鉄分限界値
鉄分限界値
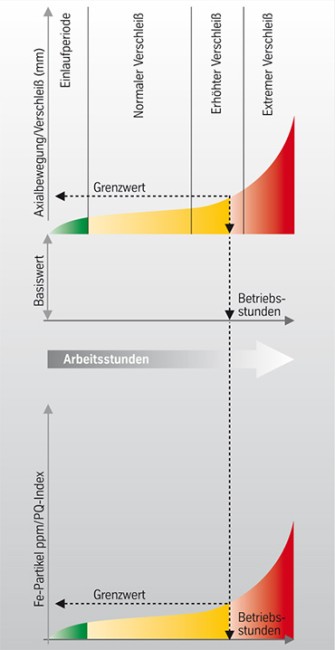
図14:摩耗曲線
潤滑剤における許容鉄含量の限界値は、稼動パラメータおよび潤滑の間隔に大きく依存します。個々のケースによっては、値は最大20,000 ppmまで許容されます。
摩耗曲線
グラフは、稼動時間に対する摩耗の増加、または鉄粒子およびPQインデックスの増加を示しています(図14)。
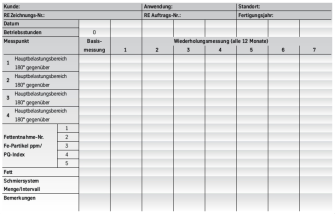
表4:測定テーブル
クリックすると拡大します
標準的な用途では、表1-3の値を参照してください。限界に達する場合は、ティッセン・クルップ ベアリングにお問い合わせください。
測定および分析値、ならびに個々のベアリングに関する情報は、別表(表4を参照)に記入し、ティッセン・クルップ ベアリングに提出してください。サンプルボックスをティッセン・クルップ ベアリングまで送付してください。
thyssenkrupp Rothe Erde GmbH
サービス
Beckumer Straße 87
59555 Lippstadt
service.rotheerde@thyssenkrupp.com
ティッセン・クルップ ベアリングは、認定された研究所にグリースサンプルを送ります。
そのメリットは次のとおりです: 分析は迅速に行われ、分析結果と摩耗測定に関する情報はメールで送信されます。
グリースサンプル採取キットは 次の連絡先までリクエストしてください。
thyssenkrupp Rothe Erde GmbH
Tremoniastraße 5-11
44137 Dortmund
電話 (02 31) 186-0
FAX (02 31) 186-2500
sales.rotheerde@thyssenkrupp.com